Welcome again to our latest webinar, how growing and midsize life science companies leverage SAP cloud ERP. Again, today's webinar will be presented by Ralph Hess VP at navigator business solutions.
Today's webinar will be a demonstration focused webinar, not all slides, actual working in the ByDesign platform. And just a quick note, please feel free to type in any questions you have during the presentation in the go-to webinar control panel, and we will address them as needed. So with that, I'm going to hand over control to Ralph and start this presentation.
Perfect. Thanks very much, Sean. And to everybody on the line here. Welcome. This is the, I guess webinars we're a bit ahead of their time in terms of presentations and meetings. So in the 2020 world, we're used to working this way now, so it's all, it's great to have you on board. Good morning, good afternoon. And at least to one of our attendees from the UK. Good evening. My name is Ralph Hess. I'm vice president of sales here at navigator business solutions. I am really happy to take you through this presentation today,
As we said, it is how life science companies are using SAP Business ByDesign, we're getting a bit more specific. Our title was how, how growing life science companies are using SAP cloud ERP. What we're going to talk about today specifically is SAP Business ByDesign, which is a solution that was very well suited towards life science. And we'll go through why and demonstrate why and how in just a few moments as we progress through the presentation. But as, as you oftentimes hear in the marketplace SAP is often intended for the large enterprise SAP 10 years ago, came to market with this solution called ByDesign. It is a pure cloud-based play. And for those who have some hesitation around cloud and validation for regulatory purposes those concerns have been allayed. And again, we'll talk a bit through that as we go through this, this presentation today.
So one of our key industry verticals, if not our predominant industry, vertical is life sciences. And so every day, Sean and I hear questions from prospective customers, they have existing customers.
- So can you do the Batch management device history? What's it
- What's the take on quality management systems?
- How do you accomplish lab testing?
- Do you support cGMP GMP?
- How does this solution support 21 CFR part 11? And oftentimes people focus just on e-signature when we're talking about that. But I think as we all know, 21 CFR part 11 is much broader in nature than just e-signature. But we address those, those broader topics as well as specifically e-signature they often talk about validation.
- Is this a solution that can be validated? Is it a validated solution? And then at times as we're in the process, manufacturing industry and life sciences they asked oftentimes about enterprise asset management, you know, preventative maintenance enterprise asset management.
So what we've done over the last three or four years, it's really bringing together both by design, with some specific implementation methodology we use with relationships that we have with various partners and with our own intellectual property to create a solution that is a really purpose-built for the life science industry. And what we've come up with is, is a pretty fancy diagram of what that means. So as we take a look at the center of what we're talking about is SAP Business ByDesign, SAP's really only cloud based ERP public multi-tenant cloud-based solution. It has a lot of functionality already in it full supply chain, support, quality and testing project management, project costing, project accounting batch tracking, serial tracking, things like that. And we'll talk about what all of those out of the box capabilities are. What we've also done though, is, is taken some of the areas where there's a bit of a white space as it relates to life sciences and developed our own life sciences package.
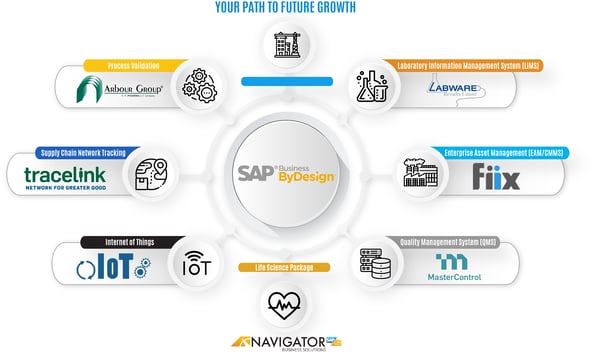
And we'll talk about what's in there. However, once we get into the life science arena, there's oftentimes concerns or questions about what about our quality management system. And so we have relationships with companies like Master Control. What about enterprise asset management, keeping track of my equipment, calibration, things like that. We've developed a relationship with Blue Mountain for, for enterprise wide asset management. Oftentimes what about testing? Well, we often times we'll integrate with lab work and we'll talk a little bit about the quality modules of by design and how those can integrate with lab work. Validation is always a very hot topic as we're speaking to our prospective customers and we have a partnership with the Arbour Group for process validation. What that means is we don't necessarily direct their activities. We have an arms length relationship because we believe they need to be a third party, but what's awesome about the Arbour Group is they have already validated a number of ByDesign systems.
So a lot of the documentation they have is already ready, already prepared for the out of the box business process that comes with SAP Business ByDesign supply chain network tracking for, you know, support of the traceability external network traceability that you that's required by the food drug safety act. We have integrations with TraceLink and then just purely with SAP and its platform. We have integration with an internet of things. So as we've talked, we, we often engage with small startup companies and they'll start with just a part of SAP Business ByDesign. And then as they grow, we will way run these additional features and functions and capabilities as it's required as the system, as the the business scale, let's take a little bit of a look at what the out of the box capabilities does. SAP Business ByDesign are, again, we will visit on a lot of this as we actually go into the software itself, but it does have features that are really key and key to a life science type companies.
Since many of them are multi-company entities, many are multi-country, which then drives multicurrency requirements. All of that is available out of the box that has the capability of managing complex supply chain. So if you're creating a medical device and you need to track that as it's going through a an external quality testing and then to an external packaging, and then bringing it back in for distribution or off to a third party logistics center for distribution SAP Business ByDesign can manage those types of complex supply chain of course, built in is identified stock, which is more commonly referred to as batching or what control and then registered products as well, which is serialization. It has fully embedded production. That's part of the supply chain that supports cGMP for both discreet and process manufacturing. And for those types of companies that are hybrid it has embedded quality control and then, and warranty tracking.
And it's a ready to validate platform. I referred to that when I, when I spoke about our relationship with the Arbour Group. So right out of the box, the system is ready to be validated and it has been validated, I guess we would call it a ready. It is a validatable platform. As we start to take a look at the compliance requirements that that are, that are required by the regulatory and statutes, we have full and complete tracking traits via either the batch or the serial number. We have user authorization and login controls and management. Every transaction is marked with the date time user that created it or changed it. A change log is maintained for for every update to a document or a master file record, the strong bill of material revision control, variance support there's integration to each QMS, which we referred to either as you know, as I had on the slide, we have that with a Master Control, also looking at building that in systems as well.
So that's really SAP Business ByDesign out of the box. As we take a look at what we have added to the overall solution to make it perhaps a more robust solution in terms of, you know, appearing to be out of the box, we have added e-signature supplier-customer product restrictions. So the whole concept of having a authorized or GMP qualified suppliers, we have the capability of, of defining those restrictions. We have a CAPA module product recalls and as the, as our diagram and indicated integration to the best of breed purpose, what I, what I call purpose-specific solutions for things like quality LIMS supply chain networking and things like that, but really the, the additional capability that we bring to the table, which isn't a product is a strong implementation team with the life science experience. We have people who have done implementations in these regulated industries and have the experience to bring to bear, to make sure that the implementation goes smoothly, that we're adhering to all the guidelines that we are taking into account all of the SLPs as we're going ahead and developing the business process or tailoring the business process to your specific needs.
So that's really enough about enough about the kind of the PowerPoint topic. Let's, let's dive into the software a little bit. So I'm going to just escape out of the PowerPoint and dive into SAP business by design. Now, I know there's some of you on, on the meeting today that have seen Business ByDesign before, for those of you who haven't I have just logged in, I am logged on with a lot of power because I want to be able to show you everything, but in order to log on, I needed a user ID and a password, which is under control of, of the system administrator, which has, you know, puts in, in effect really enforces the policy, right? So if I need to change it every 30 days, if it needs to have a certain set of characteristics associated with the password, all of that is controlled through the system administrator.
And again, starts to talk to some of the part 11 requirements. So as I'm logged on, I'm given access to only those capabilities or features or functions that are in the system. Just a very, very, very quick view. As I'm looking here, I have my launchpad that I am logged on to making it very easy for me to just access those areas that I have been authorized to. I have a larger work center list, which is a list of different work centers in the system that I've been granted access to, again, as the system administrator, I'm accessing all of them, but just as really quickly give you an idea of some of the added functionality that we build directly into SAP Business ByDesign, we have our, our CAPA, we have VCL approvals, electronic signatures. Those are all additional modules that are built directly into the SAP Business ByDesign solution.
So in terms of navigation, we can either use tiles. We can create shortcuts that allow us to be able to just very quickly and easily get to different functions within the system. Or we can use the, the search to say, Hey, maybe I want to take a look at production models. So this gives me the ability to kind of very quickly search for, for those features that I might want to access enough about that we do have a, a weekly webinar if you're interested in attending we'll follow up with an invitation to that. But what I wanted to dive into a little bit was production models, production models. As we take a look at, at a SAP Business ByDesign, and I'm just going to pull up a different one here than my standard. What we'll do is we're going to drill into this production model.
Now, as we take a look at production models, those are what is released to the floor. So as I, as I look at a production model, it is the combination of a bill of operations, a bill of operation structure and assigned product. So as we think about it, people would typically think of this product assignment to be the bill of materials, which it is, which we'll visit in just a few moments. So, as I'm taking a look at this production model, I can have different variants or combinations, which again are released under strict control that are different , different versions of the same product by bringing together a different version of a bill of operation and a different version of a bill of material. Again, we'll visit on that just a moment, but I've been taking a look at the bill of operations. I can see some information about it.
What, what the idea is, what the description is, what production site, this is valid for what the quantity is. The ByDesign solution is a task oriented solution, so that if I'm releasing a production model to a work order, this is going to tell me, how am I going to release the task that I need to confirm to execute on that work order? Who else is going to dive too deeply into that? What do you want? Automatic task printing, et cetera. So this practice is really descriptive. Again, keeping track of who created it and who changed it and a log of what those changes are. As we take a look at the bill of operations structure, you can see this, this is a fairly simplistic one. But it, it hits on the parts that I really wanted to hit on, which is the fact that as I'm taking a look at my operations, I can associate tasks to those operations and those tasks.
There can be multiple tasks within each operation. So as I'm taking a look, I'm, I have a make operation, which is to produce the product. I'm going to have report out on how much product I made, and then I'm going to have a quality check associated with it. So it's giving me also the resource ID that I'm going to use on these operations. If there's a variable duration or a fixed duration, it just gives me the ability to be able to pull together that bill of operations. As I looked at the product assignments, you're going to see now a little bit more of an exploded bill of operations and where the product is assigned. And in this weekend have either discreet or backflush type type consumption of the input materials. And again, it's just going ahead and showing you the, the capabilities of, of each of the steps within that bill of operations and the products that are associated with it.
In terms of the bill of material. We do have a bill of material and we do support five products processing. So that there's a number of customers that we have that are processed type organizations whether they be gene therapy, cell therapy, et cetera, and oftentimes byproducts need to be captured as part of that process. And then as we take a look at just some of the administrative data, we have, again, some of that tracking of that production model here, you can see that we can release a production model. Again, that's being done under, under authorization only. And we have, we can open the release planning model and open a release execution model. So we can have a planning version of this production model, and we can have an execution model version of that production model. So that gives you a little bit of an idea as we're looking at production models and you'll see that we can have different variants of the same product, and those can be in play, but only one can be a released execution model at any given time.
So that's a bit about production models. As we take a look at the production bills of material, we can just kind of drive into there and take a look at again, we'll focus on that, that particular item. You'll see that I have a production build some material. I can have different, again, variants of those bills of material. And if we just kind of drill in here and edit this, we can see the the what's on the bill of material. What, it's, what it's given this, this particular variant. I can give it an engineering change order if I want to make a change order. So if I want to implement an item change, I must select an engineering change order. And then as we're taking a look, here's a little bit of the history of those engineering change orders that, that have been done on this particular product.
Again, we have a solution that adds approval to the engineering change orders. However, if you have an external two on that, that you want to integrate with where the approval of those engineering change orders will happen we can make that happen as well. Again, we try to provide a platform upon which companies can start, and then as they build or get more complex that allows you to expand and grow into those solutions as well. So that's a little bit about the production bills of material. And then again, as, as we take a look at the production bill of operations, again, I have that concept of multi-variant. I have the ability, to define that bill of operations. So if I was to take a look, not at recently viewed, but all builds of operation by the selection, and you'll notice that I'm doing something up here, I don't have to scroll through lists.
I can just do a search using a wild card. I also can create views that I saved so that it makes it easier for me when I go into the system. But as we want to take a look at the spill of operation here, I can see how that's defined. If I wanted to go ahead and view all here, I can, I can view all in this gives me a planning view gives me somewhere use capabilities, and just gives me overall control. So as we're taking a look at how the production data is defined, we have our production bills and material or production bills of operation. We have engineering change orders, which are created based upon the requirement to change the, the production bill of material. And then we have the production models that bring those together. So really in, in terms of controlling the approval and the, you know, the SOPs and the PQs and IQs around that is documentation that is readily available. And we can add approval processing to that either inside of the business, by design, or by interacting with an external system itself and only releasing those based upon the external approvals.
So that covers off a little bit about production models itself. Let's go ahead to the next topic, which is electronic batch records with track and trace. And this is really perhaps a broader subject of traceability. And what I wanted to do was just go in and take a look at serial and batch lot tracking. So as we take a look at, and I'll start with the identified stock, which is really batch. So if you think of this is just the SAP term for a batch or a lot as I go in, again, I work at I'm going once again to take a look at my identified stock, and I'm going to look for a particular one. That's a good example. So as we take a look here at 1103,
This gives us any further. Yeah, here we go. So this is the one that I was always interested in showing you, so you can see here as I open up this batch, I can see the various transactions that have occurred against it. What I have is the ability to drill down into those transactions. That's going to give me the who's the who, what and why. And so it's, we take a look at having an electronic staff record. It's really going to be the reporting out of all the confirmation that has happened. You can see here that I did a good issue for a delivery of the product to an end customer. And I can see any of, if I was to have moved this thing around the warehouse, I would see all the different locations that, that visited. If I do a quick stock overview, it's going to show me where that product is located. And in fact, probably because I shipped it, Nope, I have it here. So I have the product and I have it in stock and it's in a particular location. So the ability to really understand a batch and a lot what's going on all the confirmations of creation, testing you know, assignment to a project that we're doing projects, that type of thing is available in the system.
So that's, that's identified stock. Let's take a look at what we call registered products. And those registered products are the are those products that are serialized. So we call them registered products, but if you have a serialized product, whether that be a, you know, a bottle full of pills, whether that be a biomedical device, they're assigned a serial number, and that would be the registered product ID. And based upon that, again, you're going to see the type of trackability traceability that you'd be looking for. So this is telling me where that is been initiated any tracking information. So this was, this was a purchase product, which we brought in and we sold. But if we wanted to do a view, all I could go ahead and see a bit more about this, which is what the parties were involved. So with the chain of custody is again, the tracking, which you would see inventory tracking.
So this is really at the location level, any changes that were made. So if I want to click here, this is first time we're seeing that change log, but on this throughout the system, you have the changes tab and you'll see that it tracks the changes who performed them when they've performed them. And then what was changed from what value to what value on each one of those particular transactions and then attachments throughout the system. We have attachments the ability to either put PDF documents, attached emails, attach links to other document management systems and the like, so that's a little bit about traceability, my apologies for taking a little while to get through a good identified stack, but nonetheless, we got there. So you could see what the content of our batch records are. What I wanted to do now is take a little bit of a look at inspection.
So as I had mentioned by the does have inspection capability out of the, out of the box I was not confused that with the quality management system, I think all of us on the phone understand that the quality management system is much larger than an ERP solution. And the quality management system is, is what your organization is actually guided by in terms of business process and having that properly documented in auditable, et cetera. What we look to do is implement the standard operating procedures, documented in your quality management system, into SAP Business ByDesign, and then through the validation services of the Arbour Group would allow you to then have a validated system from a regulatory perspective. What I want to talk now about though is ByDesign really embedded quality capabilities. So as we look at quality, there's really as I, as I look at it, we'll just go ahead and open this up a little bit and go to quality.
Notice that I'm using my, my quality search. As I take a look at any of these menu options, you can see that as I'm looking at a quality planning, I have the ability to create inspection plans, quality code catalogs, and then quality documents themselves. So as we take a look at inspection plans, we'll just take a quick look at one that we have set up for final inspection. So as you can see, I have different types of quality plans. I can perform inspections during in process inspections, final inspections from production receiving inspections. I can do inspections for delivery as well. So if I need to inspect the product prior to it going out, I will need to do an in-process inspection for production. I can set that up as well, but let's just take a look at one of the inspection plans that we have in place for the BF 1101-3.
So as I click on here, they're going to see what the definition of an inspection plan is. I don't have to pause right now and just be very clear. The inspection plans that are embedded within business by design aren't necessarily intended to be a full blown laboratory information management system, a LIMS, right, or a lab system. And some people may refer to it. It is intended, however, within the supply chain to trigger the notification that it tests needs to occur for those organizations where the quality module provides enough robustness. If you will, in terms of doing the testing, the sampling, reporting out the results, then you have something out of the box with, ByDesign that you can use. If you have a LIMS than what you would, what we would do is the quality tasks. And we'll, we'll look at those in just a moment we'll actually trigger or integrate with the laboratory information management system to indicate that there is a lab request, a test request that would then be done in the lab system, and the results returned back to complete that test or the inspection in ByDesign.
So hopefully that explains a little bit about the poll and we'll build out on that, that concept and just a minute, but as we work with the inspection plan itself, this one is just the final inspection for this particular product. We have a sampling procedure. So if I just go into edit here, we can see a little bit more about the field, but as we take a look here at the inspection procedure, I can indicate whether I want to sample records, what the sample size is going to be, what the quantity that, what the evaluation mode is going to be. So we have various evaluation mode what the number accepted is and what the inspection duration per sample is anticipated to be. This is what goes into planning. So if I have on my bill of operations and inspection step for this product, it's going to do an offset on that planning of that production work order for the duration of what that inspection is going to require.
I have my control parameters, so what's my scope of my inspection. Do I want to cataract categorize sockets inspection stock? Do I want to print inspection instructions automatically? Do I want to print sampling, drawing instructions automatically? So these are all things as you're setting up the test plan, you can actually you can actually associate, we then have quality codes, so you can create a library of quality codes which are allowing you to notate any defects or, or whatever your quality codes are, are intended to denote. I have the changes again, as we take a look at all of these kinds of controlled documents, we have the ability to maintain and manage the controls around them, any notes that are associated with it, and then any attachments that you might want to have. And again, with the ability when we're actually generating the tasks related to these inspections using the control parameters on the inspection plan itself whether it's we publish those out or not.
So that's, that gets us a little bit of an idea of the inspection plans themselves. And in terms of quality documents, this is where you can go ahead and store any of the quality documents that are going to be related to a plan. So here we just have a single one, but a in it's a Microsoft word document, but this is a place where you have the ability to store the documents that need to be associated with the quality plans themselves. And then as we go ahead into quality control, I can take a look at what inspections are being created. So as we take a look as I'm performing the transactions within, by design, so supply chain related transactions, again, whether they be a receipt in the, in, at the dock, whether it be a receipt from production, whether it be an in-process inspection prior to delivery, it's going to create these inspection tasks.
And so as we take a look at this final inspection for delivery, these would be assigned to the appropriate people based upon the routing. So you have set up in the system and then we take a look, you'll notice that every time that I'm bringing a screen up, I have obviously the header here, but I'm also bringing up kind of a summary part of the information. So as I take a look at, at this particular inspection it's telling me that it's running late. In other words, the inspection has been delayed, meaning that it hasn't been done on time. And as we take a look at it's looking for me to do quality control against this production order, what the lot is, what the size is, what the sampling is what the defects were that, that had been recorded in any decisions that would have been made.
So let's actually go into that, that inspection itself, and that's where looking at it. And you can see that we have a lot more information about it. So I have my, my logistics details. So where's it coming from? What warehouse is it in? What, as a result of what my sampling details are inspection details, decision details. Now, when we're, when we're making our decisions, we have the ability to be able to release material or restrict material. So any defective material can be restricted, that would be shown as restricted and not available for consumption or available to promise within the system that would be taking in, taken into any of the the ATP type decisions or presentation. So as we take a look at this instruction, again, this is just giving us the opportunity to, to record our results, make any decisions, give it a quality score add any attachments, any test results, et cetera, and then any miscellaneous as you take a look at miscellaneous, one of the things that it's bringing up that your document flow throughout the system, we have document flow, which allows traceability of, of both tasks and business process.
Flow, so here, you can see that this particular inspection was based upon a production order, which was generated by a production request, which was generated by a production request proposal. I'd take a look at the extended view. If there were additional details would go ahead and show that again, any of the changes that were made to this inspection, we would be capturing here. So we're just probably going to see an initiation of it. And who did it any notes, attachments, output history, if we had printed anything, we would see that output history. Let's just go ahead to general here. What's, you're also going to notice here is that I have the ability to create a CAPA case. So if I was had some non-conforming material and I wanted to create a CAPA case in our CAPA module, we could go ahead and right here and during the course of inspection, open up a CAPA case.
So that gives you a little bit of a view of what the what's, the quality capabilities and inspection capabilities are within SAP Business ByDesign. As I referred to the integration to external quote manage laboratory management systems detailed inspection quality system, it would be done at this task level. So you're seeing a task. This is a task 1399, that is an inspection. And that would be what would interface at that level with the lens of creating a request for an a, for a test, having that test then executed, and then bringing the results back into this particular task and allowing for the decision to be made based upon those tests and bringing back the relevant information that belongs in the ERP.
So that, that covers up quality. As we continue down the line here, CAPA is, is our next stop, which is, which makes sense because that's where we were. We were in quality. So let's go ahead and I'm just going to go right back to my great back to my launch pad. I have a tile for CAPA. So as we take a look, we have CAPA cases. I don't have any active, but I do know that I have active cases in the system. I also have, can take a look at all, all cases in the system. So as we look at, excuse me, any CAPA case, we can drill into that particular case. I have all the phases of the CAPA process embodied within the CAPA module, so I can initiate it, capturing all of the information. That's necessary again, if I'm initiating this out of out of an inspection, it's going to pre-populate this, but I can also create them in an ad hoc basis.
So I have the title of the external ID. You can see the type, the CAPA against what the source is, what the reported date is, the occurrence, who the owner of this, CAPA case is of what the product or process is related to detailed description report was reported by then what the due dates are. And then what the sites impacted are. So if I, if I, you know, this is just in, in this one warehouse where we have this particular site that's impacted, but we could add an additional site. If we wanted to open that CAPA for all the products across all the various sites, I then can do my risk assessment again, capturing the relevant information on the risk assessment. And then we have actually a, a button set that will allow you to complete the initial assessment. We can indicate whether containment is required from there. We can actually create a recall, or if I wanted to go ahead and create a recall on the product that was involved, I only have one of them in house. We can go ahead and do that. The investigation, we can go ahead and add various reasons for the failure create new ones, what the root cause is, what the root cause percentages complete that investigation. So really, as you can see, we're marching our way through the process of corrective action, preventative action. So now we also have the ability to create our, our implementation plan for corrective action complete that implementation, complete the review, documenting that any of the attachments related to it. And then of course our change history.
So that, that gives us as you've seen the change history, we have that ability to be able to, in this case it was initiated. So it's going to tell us what the information was that was changed based upon that creation, if anything had been changed, he would CC a change from, in a change to that's really a bit about CAPA, and it gives you an idea of what recall is as well. Something else that I wanted to make sure we touched on is we're, as we're cruising through here, we talked about recall management. So we do have a fairly straightforward screen, but something that's being further built out for recalls. So we have again, recalls that are, that are based upon CAPA cases, or we can do ad hoc recalls. So if we were to do a new one, we can create a recall ID. We would search for the products involved. We would do a research. So if I wanted to add perhaps one of our BF products here, do the research about where we, where we might have that product. I don't have any in stock, so that probably wasn't the best one to search for. Let me see if we have anything better that I might be able to show you so ahead and look at this packaging product, move that at a row.
Go ahead. We'll find that packaging product, which is a little bit better. I know we have some of those in there, and then we'll go ahead and do the research based upon, I guess I don't have any in stock anyway, that's that is the recall process of being able to identify products that you want to recall research it take a look in current stock, take a look at what's in production, and then be able to quarantine that. And last but not least what I wanted to do while we can take a look at product restrictions as well. So within the system, as we take a look in all of this kind of go ahead and open this up.
Yeah. It was a little easier that launch pad. So here we have supplier product approvals. So we, we consider, you know, some people call it GMP vendors. Some people may call it a qualified vendor list. Some people may call it a, an ASL and authorized supplier list. So we do have the ability to have an approved supplier list. And within each one of those suppliers, we have the ability to identify what product, whether it's restricted to this particular, this particular vendor, or whether it's approved for this particular vendor. And that then goes into our purchasing process so that if we have purchase requests, we can understand what we need to do based upon the status of that. Either GMP qualified or authorized supplier list and what products they're authorized for and, and create workflow around approvals and business process. Based upon that, I also have the ability to do that same thing, more, more with customers as well, right?
So we have the concept of where we may not be able to sell certain products or shouldn't sell certain products to particular customers. So in this case, again, it's kind of binary I'm approved, or I'm restricting. And I can, when it's on the outbound side to customers, I can say it's restricted to a customer restricted to a particular location, or that customer is approved. And I can also have I can also have my levels or quantities associated with that as well. So that talks a little bit about product restrictions. And as again, a week we call it, we call it restrictions, but it's really the, the supplier list and the, the customer authorization list, the final piece that I want to make sure that we touch upon, you know, I'm just going to, it's the e-signature. So as, as we take a look at e-signature within the system let me not do that. What we want to do is actually put in the purchase order,
Let's go into purchase Orders, let's do a new purchase order. And so we have the ability within the system to actually on a per transaction basis, add the electronic signature capability within the system. So as I, as I'm playing here and we'll just go and do a very quick purchase order, and if I want to just buy a particular product to bring it into stock, we'll bring in some of the,
Some of these particular product,
And we'll bring it into a particular warehouse. Bring in ten.
That's $50. If I go ahead and save this, and if I try to complete it, it's going to stop me and say that you must electronically enter and verify your pin. So again, we have this on production reporting, we have it on sales orders, we have it on the bill of material changes or eco changes. So as you're thinking about the electronic signature, we have this ability to place that electronic signature, right in directly into the user interface and directly into transactions. So that adds to your concerns about 21 CFR part 11, and as it relates to the very detailed electronic signature requiring pins and that type of thing it's, it's covered by our e-signature module.
So that's, that's a tour of really, as we looked at it, what we wanted to make sure we covered, we want to make sure we covered off the key questions. Do we do batch management? Yes. Do we do device history, which is our serial serialization or registered product, and the traceability of everything that's gone on with them? Yes. Do we have quality management? We talked about that. And, and how we can interact with quality management or how you can implement elements of quality management within ByDesign. We talked about the concept of the task, triggering integrations with lab testing. We have the full support of GMP, both through the documentation, the authorization of suppliers, and vendors, having specific business process bills of operations control over those bills of operations, filter material, and production model 21 CFR part 11.
We hit all of the various elements of that, that regulatory environment. We talked about validation. We didn't talk too much about enterprise asset management, but that is something that we'll have one of our partners come on in and do a full presentation and a webinar on that. But for now, I think we're now to the point, Sean have we had any questions, not, we haven't gotten any questions through the presentation. I know we've run a little longer than we expected. Are there any questions out there that we haven't touched on, or Ralph hasn't touched on during his presentation?
I'm not seeing too much right off the bat, but what we'll do is let's leave it there and say, thank you very much for attending the webinar. Hope. Hopefully, you found it insightful on how ByDesign and navigator. It works smoothly together for the life science organizations. And what we'll do is we'll follow up. We'll reach out to you and have direct conversations with each of you to see how we can best help your organizations with that. I want to just say thank you, Ralph, for taking the time. Thank you attendees for taking the time to be with us have a great afternoon, enjoy the rest of your day, and stay safe. Thank you very much.